Andebit et beaqui corendit, ut quostes esciendion re dit ad et prae parion es quia quas alibus sam, omnim faciden ducipidiat arum autem nobis enis es voat

5. Driving to the Penfield Homestead Museum via Creek Road
Iron Processing Technology Develops
Listen to the Iron Story Site 5 Audio Narration Here
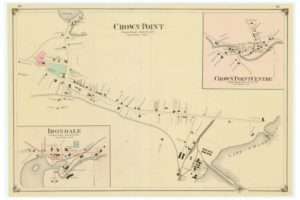
Towns like Moriah and Crown Point developed the self-sufficiency that early inhabitants needed for a successful settlement. They built grist mills to process grains and sawmills to provide lumber to build the mills and houses. Iron was needed in the building of those facilities and for farming tools. Commercial mining ventures appeared in Essex County in the mid to late 18th and early 19th centuries. However, small-scale iron mining and manufacturing were common too. Farmers and other locals would mine and work iron found on their property for supplemental income or produce tools and farm equipment. All of this required water power, and in Crown Point, that source was Putnam Creek. In part due to its significant vertical drop, it became an industrial river, powering upwards of 100 water wheels at mills over its seven-mile course to Lake Champlain. Each of the major water power sites along the creek provided the nucleus for a hamlet. Water-powered wheels that milled grain for flour, spun wool, cut timber into lumber, ground bark for tanneries—and hammered impurities out of smelted iron.
Making Iron
No matter the technology or type of iron, one requirement is universal. Before iron can be transformed into any usable product, it must first be separated and then either smelted or melted. The fourth most abundant element on the planet, iron exists naturally as iron ore, which is an oxide of iron—this just means that iron has a natural affinity for oxygen and likes to bind with it. Iron ore also contains a variety of other chemicals, such as sulphur, silicon, and phosphorus. To remove these “impurities” and get just the iron from iron ore, the oldest and most primitive method was to smelt the iron, reducing it to a softened state. Historically, this was accomplished in small quantities in forges—most commonly the Catalan forge, which was developed in Spain in the eighth century, but commonly used until the 19th century. A Catalan forge is essentially an oven that is able to resist the heat of the charcoal that was used for fuel. Charcoal heats the forge, then iron ore is added, and more charcoal is added to the forge. As iron ore heats, the oxygen is released. The end product is called a bloom—a spongy mass of iron and the unwanted, non-iron bits known as slag. The slag separates from the iron into distinct chunks. And that’s where the water-wheel-powered trip hammer comes in. This large, powerful hammer pounds out the molten slag from the iron. Sometimes a form of limestone called flux was added. It reacts with the sulphur in the ore to help remove impurities and form slag. The end product of the forging process is wrought iron, as in “worked” iron. This is the iron that could be shaped by a blacksmith into finished products like nails, chains, horseshoes, and ornamental workings. In the early days of the railroad, wrought iron was used to make the rails. However, it was quickly recognized that a better material was needed as wrought iron rails were too weak to carry the loads and did not last long—particularly when trains traveled at higher speeds. It was in fact, in part, this weakness that drove the technology for a stronger alternative.
From Smelting to Melting
A more sophisticated method of ironworking would actually melt the iron in a so-called hot blast furnace. Because blast furnaces get much hotter, the iron becomes molten or melted. This causes iron to absorb more carbon, resulting in what’s called cast iron. The melted iron runs directly from the base of a blast furnace into a sand trough that feeds a number of smaller troughs perpendicular to it. This configuration was thought to resemble a sow suckling a litter of piglets, and so the product was called pig iron. Cast iron could be cast directly into molds at the blast furnace or remelted from pig iron to make other products. Another type of furnace, the cupola furnace, was typically used in tandem, as it was used to re-melt cast iron for other products. Both smelting and melting remove slag from iron ore. The blast furnace is bigger, requiring more charcoal to heat. However, it also made it possible to produce higher quantities of refined ore. Hot air pumped into the furnace through a pipe could control the temperature of the charcoal, which can reach more than double the melting temperature of iron. In the Adirondacks, the thirst for charcoal was insatiable. As the surrounding trees needed for making charcoal disappeared, coal mined in Pennsylvania was substituted for charcoal. The trains and canal boats sending iron ore and pig iron south returned with anthracite coal.
CLICK TO ADVANCE PAGE TO SITE SIX